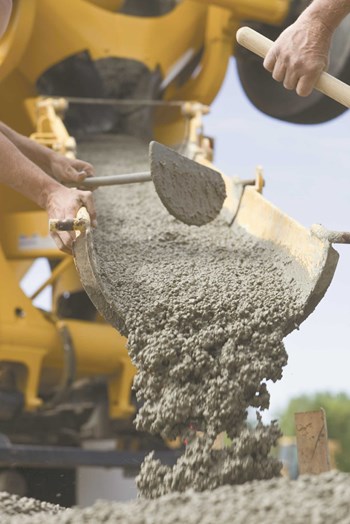
Freezing, thawing and deicing undoubtedly take their toll on concrete during typically harsh New England winters. Corrosion of concrete is an issue in the Northeast, and homeowner associations need to ensure that the concrete forming their sidewalks, pavement and parking lots, as well as walkways and balconies, is properly installed and maintained.
Concrete Facts
Concrete is a mixture of four basic components: rock, sand, cement and water. A concrete mixture is similar to cake mixes, said Greg Stratis, manager of Shea Concrete Products in Wilmington, Massachusetts. “You can go down a supermarket aisle and see many different recipes. With concrete mixture, it depends on the application of where it is being used.”
“If you are looking for a product that can handle heavier car or truck traffic, concrete is the best product,” he said. “The only other product that you would consider would be asphalt. Concrete would be better because if the sub-base beneath it crumbles, it won’t deteriorate they way asphalt would. Asphalt relies a lot on the prep work for its strength whereas concrete doesn’t.”
“Concrete is by far and away the best product for heavy duty pavement applications,” said Jon Kuell, executive director of the Northern New England Concrete Promotion Association in South Portland, Maine. “As far as strength and durability, concrete has no equal.”
Dan Clark, president of the New England Chapter of the International Concrete Repair Institute (ICRI) in Woburn, Massachusetts agrees. “Concrete offers the highest compressive strength for a pavement surface. Concrete has the strength to deal with the incredible point loads that come from tires as trucks and heavy vehicles turn and maneuver,” he said. “You will notice that at airports, freight terminals, and the receiving areas of your favorite box stores the pavement of choice is concrete. Concrete is subject to expansion and contraction based on temperature and exposure to sunlight, as is any paved surface. The benefit to using concrete is that the surface of your concrete pavement does not soften and lose its strength from this exposure.”
New formulations and technologies have come along over the years that have improved the performance, appearance and life span of concrete and pavement.
The mission of the National Concrete Masonry Association in Herndon, Virginia is to advance and support the concrete masonry industry through research and education programs. “Through our NCMA foundation program we have given out thousands of grants,” said Michael Maroney, a production specialist at NCMA. “Once a year we get grant requests and the engineering staff will sit down and go over them and check recommendations. We’ve given out grants for a life cycle study of concrete and research on concrete’s environmental impact and grants on ways recyclable materials, aggregates and admixtures can prolong the life of concrete. Concrete is constantly evolving.”
In 2003, the Yangtze Dam Project (a hydroelectric dam that spans the Yangtze River) in China, inadvertently started a concrete research frenzy, said Maroney.
“During the building of the Yangtze Dam, China was paying top dollar for cement being produced in the United States,” said Maroney. “What happened was that it kicked off a renaissance. People began to think ‘how can I make concrete not only better but more efficient?’ People started experimenting with different things and looking at alternative materials like granulated furnace slag. The whole green movement began happening with concrete.”
Improved Performance
“Technology has definitely improved the performance of concrete. The use of concrete admixtures is a science in and of itself,” said Clark. “Concrete admixtures can allow for hot or cold water applications of concrete to insure proper installation. Admixtures can be added to provide waterproofing, protection of the reinforcing steel and increase the performance of concrete relative to freeze and thaw cycles.
Concrete powers a $35 billion industry in the United States and employs more than two million workers across the country. Over 55,000 miles of concrete spans our nation’s highways. Reinforced concrete, pre-stressed concrete and precast concrete are the most widely used types of concrete.
“The greatest enemy of concrete is the intrusion of chlorides (road salts). Chloride -resistant admixtures can be added directly to the concrete mixture at the plant,” said Clark. “And joints should be sealed with a joint sealant to protect against water intrusion. Once concrete has been placed, finished and properly cured, the application of a clear, penetrating sealer will add years to the life of your concrete.”
“Occasional sealing is necessary to protect concrete from deicing operations. If this is done, it will certainly extend the life of concrete,” said Kuell. “But the best way for prolonging the life of concrete pavements is to use it for what it was designed for in terms of traffic loads.”
Concrete parking lots are designed based on anticipated vehicular loads, volumes and soils condition. Concrete pavement thickness can range from 4.5 inches to 7 inches. The contractor or designer specifies the strength of the concrete, such as 1,500 psi (pounds per square inch) for curbs or landscape borders, and up to 2,500 psi typically for sidewalks, stoops, or patios.
For house foundations or condo building foundations, one would typically need 3,500 psi concrete, and for pavements that support traffic, the industry recommends 4,000 psi, said Matthew Koerner, president of Manhattan Concrete Design in New York City. “Anything beyond 4,000 psi would get into structural concrete,” he added.
“Most concrete pavements for a typical house or condo foundation will be in the 3,000- to 5,000-pound compressive strength range, depending on the application,” said Kuell. “An engineer should be employed to determine the best concrete for the given application. AC1 318 and 1BC guidelines for buildings and AC1 330 for concrete parking lots should be followed.”
The owner or developer should require the contractor to be an American Concrete Institute Certified Flatwork Finisher. These finishers offer concrete construction knowledge, skills, and equipment to get the job done right, as well as guidelines. ICRI standards are written into all specifications.
“Maintenance should start at the beginning,” Stratis said. “After the concrete is poured and placed. There’s a variety of types of sealants you can use. There are hundreds of them out there depending on the type of concrete. A sealant is a clear liquid that usually absorbs into the concrete. The type of sealant you use depends on if it’s vehicle or pedestrian traffic or if it’s a harsh environment. You can use sealant once a year or every five years. It’s like paint. If you use good quality paint, it’ll last a lot longer than an inexpensive one.”
Maintenance Matters
The two most common problems or maintenance issues associated with paved surfaces are cracking and spalling, said Dave Dimmick, the executive director of the New England Concrete Masonry Association in Manchaug, Massachusetts. “When you see small micro-cracking in the surface, that is spalling and it’s a sign that concrete is starting to crumble,” he said. “When you see spalling, you should add sealant immediately.”
“To maintain horizontal concrete, the best practice calls for the scheduled application of a penetrating sealer. Try to keep the concrete clean and free from oils and road salts. Address any cracks and make sure construction and control joints are properly sealed,” said Clark. “For vertical concrete the same holds true, though in protecting vertical, above grade concrete, in addition to clear, penetrating sealers there are many aesthetically-pleasing waterproof coating materials available.”
Kuell suggests that a maintenance schedule be established to inspect and seal the concrete every few years, or whenever the owner deems appropriate given the demands of the pavement and the climate it is located in. “A representative from the ready mixed concrete industry also has tools to help owners and engineers assess the life cycle costs associated with maintaining concrete pavements through the use of National Ready Mixed Concrete Association’s Concrete Pavement Analyst software,” he says.
Some sidewalks are also not designed for vehicular traffic. The sidewalk that crosses the entrance of a parking lot should be thicker. A thicker-than-necessary pavement, though, costs more to install.
One of the common failures that can occur on a concrete parking lot is around drainage structures. Inadequate compaction of backfill material around these structures can result in loss of support for the pavement.
Municipalities have different specifications for inspections throughout New England. The Department of Transportation oversees highways and roads. There are also paid consultants who act as inspectors for properties, said Stratis.
Concrete Problems
Problems can result when the pavement is not strong enough for heavy loads such as garbage trucks and utility vehicles or when pavement or sidewalks are displaced. The roots of a tree, for example, can lift pavement. When one section of pavement becomes displaced, it becomes an automatic slip-and-trip hazard. This is of particular concern to buildings and HOAs with elderly residents.
“Trip and slip lawsuits are common,” said Bill Shaheen, a personal injury lawyer based in Dover, New Hampshire. “It could be from a slip or trip caused by wet surface, ice, snow build-up or a pavement crack. There are all sorts of things that can happen if things aren’t done to code.”
“There is a legal duty on the part of a residential building to maintain their property in a reasonably safe condition,” added Shaheen. “Their legal duty is to residents of the building. If they know there is a hazard in the common area and they don’t fix it, they are liable. If it is known that there is a danger to people who will use that common area—then they have a duty to repair it.”
Whoever gets injured on the property, the homeowner’s policy or the building’s policy comes into play. The guest could have a claim against the homeowner and a lawsuit could get filed for negligence in failing to maintain the property in a safe condition. The contractor could also be liable if there was a construction defect.
Injuries on property can result in civil action filed in the appropriate municipality against the building ownership. If there is a violation of code it can be used in a civil trial as evidence of negligence.
Shaheen recently settled a premises liability case for $275,000. The claimant was working as a delivery man delivering items to a supermarket in Southern Maine. When he was leaving the store, after delivering the items, he fell on a crack in the ramp leading from the building. He suffered severe knee injures and required several surgeries.
In order to avoid expensive litigation, Shaheen advises building owners to do periodic, reasonable inspections of the premises and to keep common areas clean and safe. If there is a crack in the concrete, set cones up so no one can trip and fall, and then make repairs as soon as possible. “Whenever you invite people onto your property, you have a duty to keep it in a safe condition,” he said.
Peter Malbin is a freelance writer and a contributor to New England Condominium. Editorial Assistant Christy Smith-Sloman contributed to this article.
Leave a Comment