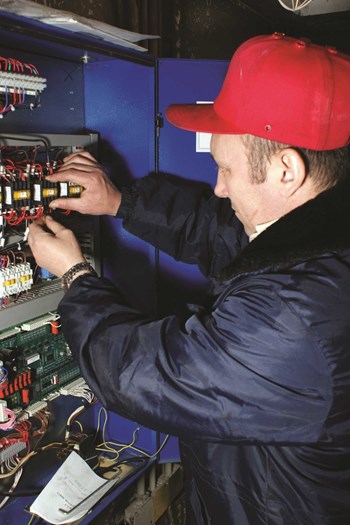
Every resident living in a building with more than two stories understands the convenience an elevator affords. While antiquated forms of the modern elevator date back to Ancient Rome, the first passenger hydraulic elevator was installed in New York City in 1857. Since then there have been many updates in the industry.
“Looking at elevators from a hundred years ago to today is like looking at a Model T opposed to a 2011 car model,” says Brian Black, a code and safety consultant for the National Elevator Industry Inc., a national trade association representing the interests of firms that install, maintain and or manufacture elevators, escalators, moving walks and other building transportation products. “In the last 20 or 30 years, the biggest change is that all elevators are computer operated. So often, performance is based on the software and how it interfaces with the machinery.”
If properly maintained, the majority of elevators have a life span of 20 years; in some cases, newer models can have a life cycle exceeding three decades. For those high-rise buildings with older elevators still in operation, maintenance issues are often experienced for a handful of reasons. In some cases, parts are outdated or companies have gone out of business.
“Most of the older elevators in mid- and high-rise buildings have the old mechanical relays. These older systems are prone to breakdowns and they are getting harder and harder to get repaired,” says Michael Pasquino, senior portfolio manager for Barkan Management Company in Boston. “These constant breakdowns start adding up in cost. Parts are getting hard to find. When an elevator company does a replacement in an old building, they keep many of the old parts to use on elevators with these old relays.”
Safety First
According to Consumer Watch, there are an estimated 900,000 elevators in operation in the United States, each serving an average of 20,000 people per year. This equates to 18 billion passenger trips per year. As with all statistics involving transportation of humans, higher frequency results in more accidents.
The U.S. Bureau of Labor Statistics and the Consumer Product Safety Commission found that approximately 27 people die each year in elevator accidents. There are an additional 10,200 injuries from elevators. The majority of these accidents are related to elevator door malfunction, carriage misalignment with floors and passenger safety issues.
In order to ensure that elevators are operating safely, rules and regulations are in place; however, these vary state by state. “There is an acceptable performance standard based on annual inspections and certificates,” says Gregg Laufersweiler, sales and marketing manager for the Stanley Elevator Company. “It depends on what state you are in. In Massachusetts, it is performed by an elevator company and a certified inspector. In New Hampshire, mechanics receive an inspector’s license without a state inspector required to be present, and in Maine, it is a third party which is not the state or the elevator company.”
While an annual inspection is required, the industry standard for safety and maintenance was developed by the American Society of Mechanical Engineers. The Safety Code for Elevators and Escalators, an exhaustive list of requirements, is available online. “In short, all the safety circuits are checked. Every five years the elevator is tested for load, speed and buffering,” says Laufersweiler, adding that other annual tests include “elevator drops” to make sure the governor is working properly. The governor is a pulley that rotates when the elevator moves.
Unlike automobiles, elevators and elevator parts are not subject to federal accident inspections or parts recalls, notes Consumer Reports. As a result, there is little information regarding elevator defects available to the public. If a product problem or defect is identified, the manufacturer is only legally required to send a certified letter to equipment owners. This can create a gray area for condominium boards.
Since every state requirement is different and there are no federal regulations, building managers and superintendents may or may not be involved in the technical understanding of the elevator operating system. “I think most building managers look to their elevator companies to be the experts and tell them the code requirements,” says Pasquino. “When installing a new elevator, most management companies hire an expert to write the specs, bid out the replacement and oversee the installation of a new elevator.”
Regardless of state, all elevator inspectors are put through rigorous training. “In New England states, all state inspectors are certified which involves extensive training. They are required to complete a one year apprenticeship before they are certified,” says Black. “After that they must enroll in continuing education to maintain that certification. So, New England has a fairly high level of requirements.”
Inspection and Maintenance
With inspections required every year, with subsequent inspections every three (for commercial elevators) or five years depending on elevator and state requirements, it is essential to have a maintenance schedule that not only ensures proper performance but limits the risk of accident or downtime for elevators that fail inspection.
“Where condominiums boards and owners run into problems is when maintenance contracts lapse,” says Black. “It’s similar to changing the oil in your car. If you don’t change the oil for two years you will run into problems and the same goes for elevators.”
When issues are found during inspection, there are protocols in place to address them so that elevators are back in operation as quickly as possible. “If a problem is found or if a new code requirement comes into play, the inspector will notify the elevator company and a certain amount of time will be given to make the repair before the elevator is re-inspected,” says Pasquino. “The elevator company will notify the manager of the issue and cost to implement the change or repair.”
A yearly inspection is similar to a car inspection in that it has to be completed within the same month as the previous year. The majority of code violations are seen as easy fixes—although in some instances, elevators will be shut down until the inspector gives his or her seal of approval. “While in some cases there is a grace period for inspections, most are completed routinely,” says Laufersweiler. “If problems are identified, there is a time period allotted to correct the problem and that varies from state to state. In Massachusetts, for example, it’s 90 days, but if it is a safety violation it has to be fixed immediately.”
Examples of non-safety code violations include using an elevator for storage, which is a fire hazard; non-working emergency lights; or standing water at the bottom of the shaft (pit). “These are owner/operator issues that are easily addressed,” says Laufersweiler.
There are a number of maintenance contracts to select from and these include a full maintenance contract; parts, oil and grease contract; and oil and grease (examination and lubrication) contract. The majority of contracts selected by commercial buildings are full maintenance contracts as the elevator service company assumes all responsibility for the equipment. Essentially, it is an insurance policy allowing building managers to budget yearly costs while eliminating liability and exposure to claims in the event of accidents or injuries.
“Regardless if an elevator is two years old or fifty years old, the key to safety is proper maintenance, and a building needs to find a company that is reliable and does the job well,” says Black. He notes that there are a number of organizations that provide guidance for property managers and boards.
Before entering a maintenance contract, for example, elevatorsource.com suggests asking the following questions:
• When does overtime apply under the contract?
• What are the differences between overtime trouble calls and overtime repairs as they relate to the contract?
• Is travel time a consideration because of location or union agreement?
• If maintenance is missed or incomplete are you entitled to a refund for that month?
• Do trouble calls count as a regular monthly service call?
• What is the response time for a trapped passenger?
• What is the availability of spare parts?
It is important to note that most maintenance contracts do not cover the following:
• Overtime callbacks / trouble calls.
• Doors knocked off tracks by movers.
• Keys dropped in the pit (you may be surprised at how often this happens).
• Debris in car or hall door sill tracks.
• Foreign objects caught or wedged under car or hall doors such as carpet tacks, small rocks and coins.
• Stuck buttons and broken safety edges.
• Flooded machine room, top of car or pit.
• Vandalism: doors kicked off tracks, fire in elevator cab set by vandals and burned car buttons.
• Calls placed for service resulting from building power even though no emergency power feature exists to run the elevator equipment.
• Elevator telephones and phone monitoring.
With regard to costs for maintenance contracts, prices “are all over the map,” says Black. “It depends on the size of the buildings (how many floors) and the equipment that is used. Today elevators can be monitored remotely, so if there is a problem often it can be handled quickly.”
The majority of maintenance contracts can be broken down to 80 percent labor and 20 percent parts. The majority of contracts are for five years with many requiring owners to pay for services 90 days in advance. These contracts can be amended and generally require 90 days’ written notice to alter or terminate.
“The bottom line is that anything mechanical has to be maintained—and while it is costly, in the long run it saves money and extends the life of the elevator,” says Laufersweiler.
W. B. King is a freelance writer and a frequent contributor to New England Condominium.
Leave a Comment