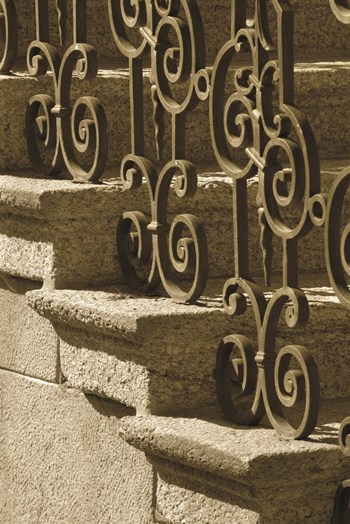
American history is littered with tales of ornamental metal work dotting Boston’s architecture. From railings to cornices to balconies to windows, decorative metal was all the rage in the late 1800s and early 1900s, but has taken a backseat to both stone and brick in the days hence. That said, there is still a place for metal to be used in a purely stylistic fashion amid the condominiums of New England, and various architects and craftsmen are both reinventing the form and adhering to the classic styles of yore, all in effort to keep an area known for its vibrant residential work alive and well.
“I think that, as a designer, we try to keep things a little more simple these days,” says Marc Hershman, a principal with MSH Architects in Newton. “There’s an over-concern that too many objects that protrude from a façade, when combined with inclement freezing weather, can be problematic.”
Some explanation for the decline of ornamental metal work can be attributed to the economy, as these types of designs tend to thrive in boom periods, when the economy is robust. As Hershman says, “you would have more ornament or more exploration of unusual detailing on the public buildings where you have this luxury of budget, and the end user isn’t a collective of numerous clients.” The very nature of a home owner’s association prohibits extravagant spending on decorum, metal work included.
That said, the areas that do have somewhat of a deeper purse at their disposal are those most likely to still court decorative metal work. Chad Allen, project manager at DeAngelis Iron Work in South Easton, cites Cambridge, Wellesley, Weston, Marblehead and Swampscott as some such areas. And architect Alfred Wojciechowski, principal of CBT Architects in downtown Boston, specifically pinpoints Back Bay as a hotbed for ornamental metal work, both classic and contemporary.
“In Back Bay, you’ll see much copper as used to create ornamental cornices,” Wojciechowski says. “There’s copper work on the roofs and bay windows. You’re likely to see a tremendous amount of copper as an ornamental metal there, as well as around Commonwealth Avenue, Marlboro Street, Beacon Street and Boylston.”
The Make of the Metal
Much of the reason that craftsmen specializing in metal work still thrive in Boston is due to historical preservation. According to Wojciechowski, the majority of the metal work installed within the areas mentioned above was put in place over a century ago, but its resilience is a testament to those tradesmen who make it their specialty to preserve the styles of yesteryear still today.
“We have a very robust copper industry in the Boston area because of historic preservation,” says Wojciechowski. “Just to use Back Bay as an example, at one point a building’s fabric would have been destroyed, and the cheapest siding that you can imagine was put in to replace it. When those buildings—which operated as rooming houses in the 1960 and 1970s—are being restored to high-end condominium properties, they’re reintroducing higher quality materials into the mix. In regard to restoration, they’re actually mandated to return to the original quality materials. The roofs, bay windows and other accoutrements all contain beautiful ornamental metal work, which works in both historical and luxury capacities.”
Aside from copper, Boston-area ornamental metal is composed of wrought iron, cast iron, steel, aluminum and various galvanized materials, according to Allen and Hershman. Stainless steel and aluminum are the primary components used from a purely decorative standpoint, while alternate metals have a more ingrained relationship with a building's structure.
In newer residential projects where metal is being used, Hershman observes much implementation in "creative balcony work, protruding in or out of entry areas and in cornice roof lines. Also in roof line extensions, possibly around windows. But, especially in regard to multi-unit building, people are really leaning toward restrained detailing these days," he says.
Allen notes an uptick of metal work in the area surrounding Harvard University. "We're actually renovating some undergrad dorms now, and they're using more steel for finish," he says. "We do a bit of high-end residential, where there's definitely more metal work—bronze, stainless steel. The latest material to see a surge over the last five or ten years is corten steel, which resembles a mill finish, and actually benefits from rust. It's normally used for bridge steel. One allows the exterior of the material to oxidize and rust. This seals off the inside of the material, and then the corten stops rusting on the exterior once it has a surface coating applied."
There is interesting metal work happening outside of the higher-end properties as well, Wojciechowski explains. "When you get into the smaller scale condos, in Cambridge or Kendall Square for example, you'll see another layer of iron work on balconies or terrace enclosures. These products are custom-made, and all of the posts that hold the pieces in place will be assembled by a craftsman. The craftsman will purchase a pre-designed woven metal fabric, which are industrially produced in a very exacting and interesting way, and these can be very beautiful despite not being made specifically for a particular railing."
Trying to Maintain
One perk of ornamental metal work is that an attentive and responsible property manager can count on it to remain durable for many years without any significant renovating. Stainless steel, to cite but one example, requires about as much maintenance as brick, according to Hershman. However, it is prohibitively more expensive than the alternatives.
"Stainless steel does become fairly costly," he says. "But less durable metals can become problematic as well. We actually do retrofits where we remove parts that are difficult to maintain, and replace them with more durable, less expensive materials. Especially with residential construction, more modest and more traditional construction is seemingly the way to go right now."
The major threat to exterior metal work, given the Boston area's famously harsh winters, is that finishes break down, paint wears off, rust cracks, and rails become deteriorated, according to Allen. In his work with Harvard, he notes that the school meticulously restores its metal work every twenty years. "Every building on campus is a 75-year-old building, at least, and they're pretty good about restoring stuff on a fairly regular basis."
Aside from relying on an outside vendor, managers and associations can take steps to care for their metal work on their own. Allen recommends re-painting every three or so years, as not only the aforementioned harsh weather, but UV rays from the sun will break down paint over time.
And Wojciechowski expounds upon the virtues of copper. "Copper is about as maintenance-free as you can get," he says. "It starts out as a bright orange, becomes a dark brown after a few months, and then eventually turns into a green, which takes a decade or longer, and then it settles into a stabilized green for another century or so."
Outside of the weather, the way in which decorative metal work is used plays a part in how long it can survive without major renovation. As Wojciechowski explains, if an adult is occasionally leaning up against a balcony rail with a cocktail after a long day, that rail could survive 20 to 30 years sans serious work. But if there are kids involved, sliding up and down a railing like a pack of ragamuffins, the metal will wear away significantly faster.
What's Next?
As stands, architects like Wojciechowski and Hershman both note a subtle breaking away from the classical style of old Boston, as designers seek to use ornamental metal in more contemporary, cutting-edge ways. However, this does not mean that the balconies, cornices, and window work of earlier centuries will fall by the wayside.
"I think that the world of contemporary design has permeated across the board," says Wojciechowski. "People are looking for fresh ideas, rather than replications. Folks who love historic properties tend to move into authentic historic buildings, while newer towers tend to be very sleek and contemporary, providing abundant natural light, terrific vistas, cleanliness and top-shelf modern amenities. The middle ground has kind of vanished between these two ideals."
Hershman acknowledges that he hasn't witnessed any sweeping change in the residential real estate market over the last three or four decades. "The grand mid-rise residential properties have over time been converted to condominiums, so we're seeing a lot more adaptive reuse projects aimed at maintaining existing housing stock than we are an increase in new high-rise and multi-unit construction," he says. He also observes an uptick in mixed-use residential with retail, but notes that many such projects feature more masonry than ornamental metal work.
Allen, on the other hand, points to 2002-2007 as a period of upswing in residential design—and one that may point to future trends, as the economy rebounds from the financial downturn of the past decade. "In those years, architects were experimenting with different kinds of metal work, different finishes—they were interested in something new," he says. "All kinds of projects were being commissioned, from stainless steel retaining walls to bronze retaining walls, bronze or stainless steel pool gates, stairs made out of everything from steel to glass treads, different finishes from patina polish to corten."
So while glass, brick and stone have recently made more of an impact than metal work in residential exteriors, Boston's deep well of talented craftsmen will undoubtedly continue to innovate the way condominium and residential properties look, with ornamental metal serving as but a single tool upon their well-stocked belts.
Mike Odenthal is a staff writer at New England Condominium. Freelance writer Lisa Iannucci contributed to this article.
Leave a Comment