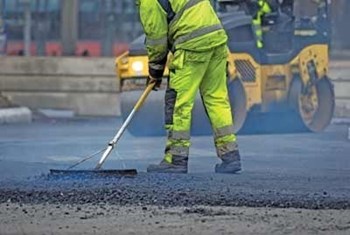
When the days finally lengthen and the mornings lose that bitter chill, it’s time to assess the damage wrought by another New England winter. For the board members and the property manager of a community association, that wintertime damage can be found throughout the property, from the landscaping and roofing to the tennis courts and, yes, even the parking lots.
The rain, ice, snow and salt that bombard a parking lot during the winter months can take a heavy toll. Cracks can form or spread. Potholes can appear and grow. Stone and chunks of pavement can break loose. Painted lines can wear and fade. Or a combination of all these things can happen at once. For a property manager alreadydealing with other spring clean-ups and repairs, a down-and-out parking lot can be a major headache and a costly repair.
Assessing The Damage
The first step is to inventory the damage done over the cold, icy months. “After each winter, walk the lot and seewhat you can see,” says Craig Swain, president of New England Sealcoating in Hingham, Massachusetts. This also may be the time to call in an expert to not only tally up this year’s needed repairs but to create a long-term plan of attack. “Most pavement companies will send someone out and create a maintenance program for you,” says Swain. “They can tell you what you need right now, and they can tell you that two years from now, you’re going to need new seal coating.”
And with a long-term plan in place, current repairs can begin. Among the most common work done, cut-and-patch jobs will target specifically-affected areas. The “cut-and-patch” technique, for example, may be used to fix a pothole. Work crews will saw cut or jackhammer out the damaged areas, going at least a foot beyond the edges of the “injured” pavement, beforeputting in new processed stone and covering it with a thick coating of asphalt. They’ll then seal it tight.
“Overlaying” is another repair – and preventative – measure. Bob Burns, owner and president of Burns Associates – Engineers, based in Portsmouth, New Hampshire, encourages managers to be careful with overlaying and ensure that it’s not simply being done as a quick fix. “Going over the lot with new asphalt can be a waste of money,” he says. “It can create reflexive cracking. And by just paving over problemareas, you’ll often see those cracks come right up again through the new coat.”
Swain agrees. “If there’s cracks, then you’re just covering up the problems and you’ll end up with the exact same lot, only higher,” he says. “With overlaying, you’re basically just trying to get an extra year or two out of the lot.” If the lot is in good shape overall though, and “you may have just a few dips and doodles,” then a new overlay might be fine, he says. Just make sure the job is handled properly.
If there’s a small divot that needs repairing, for example, make sure the contractor does not just pave over it. Make sure they cut a groove out so that the new pavement does not stick up above ground level and get caught by snow plow blades the next winter, Swain says.
Crack Filling
According to Swain, crack filling or sealing is another common and vitally important type of repair. “Next to filling pot holes, crack filling is the most important preventive maintenance that can be done,” he says. There are all types of crack fillers, but Swain encourages property managers to make sure their contractors are using a flexible filler that is applied hot, not cold. Watch out, too, that they are removingall of the grass that has grown in the crack. That does not mean simply pulling out a few weeds, he says. “You need to have a compressor to blow every root and leaf and anything else trapped in that space.”
And finally, seal coating can help beautify as well as protect pavement. “Most people love how it looks, but what you’re doing is protecting the pavement from water, gas, oil and most importantly, you’re protecting it from the sun,” Swain says. “Over time, the sun can dry out the pavement andremove its flexibility.” To best protect a parking lot, Swain recommends seal coating when it is about a year old in order to protect it from the sun as soon as possible.
Each seal coating, Swain says, should be designed specifically for each particular lot. One area might need only one coat while another, more heavily trafficked area might need three. It shouldnot simply be a “one size fits all” fix.
Stopping Damage Before It Starts
Looking ahead, what’s the most important preventative measure a building can take when it comes to its community parking lots? “Do your maintenance before winter starts,” says Burns. “As the saying goes, ‘an ounce of prevention is worth a pound of cure.’”
In particular, Burns says that means investing in proactive crack sealing “once a year, every year. That’s not excessive. If you wait instead for small cracks to become larger, it could be too late.”
Crack sealing, Burns says, will help prevent routine water infiltration, which can loosen the pavement’s subgrade and the soil below. “If the water gets down there, it will loosen the soil and without firm support, it will allow the pavementto flex. At that point, whole sections can move, settle or heave during the winter. And then you may have lost that whole section of pavement just by not spending a few pennies before winter started.”
Swain agrees that preventative maintenance is key. “Trying to keep water out of cracks and prevent it from reaching the sub-base to avoid wearing away that base is very important,” he says. Filling cracks and repairing potholes before the harsh winter elements set in can go a long way toward havinga better, less expensive spring.
Another key ingredient to a long-lasting, healthy parking lot is adequate drainage, says Burns. “You want to make sure that the drainage underneath the pavement or going through the subspace is good,” he says. “You want to make sure it’s draining down and away from your lot. Keep your culverts clean. Go out each fall and make sure all the drains and catch basins have been cleared. If not, your parking lot could become flooded. It all goes back to that idea of an ounce of prevention.”
New, “Green” Approaches
These days, new products are constantly coming to the market, including “green” pavement preservation and repair materials. A new material called Sun Shield is designed to help reduce heat on pavement and can helpa building meet LEED requirements. The downside? “It is very expensive,” says Swain.
Geo-textiles are another new development, designed to cover over cracks. According to Burns, “it’s not 100 percent effective and not all pavers willuse it.” For an association looking for a new approach, however, it might be worth an inquiry.
While the demand for eco-friendly paving materials is still in its infancy, manufacturers believe that will change as federal, state and local regulations and standards evolve. Michael Wohlfahrt, New England account executive for Unique Paving Materials based in Cleveland, Ohio, says that his firm anticipates that those tighter restrictions will be coming soon to the industry. As a result, Unique Paving Materials recently released a new permanent patching product called UPM Green that has zero volatile organic compound or VOC emissions. These VOC numbers are regulated by the Environmental Protection Agency and paving products must meet minimum standards on emissions. Unique PavingMaterials exceeds these standards, he says, with their zero emissions.
Part of the issue in promoting or encouraging the use of green paving products, Wohlfahrt says, is that no one has really defined what “green” means in the industry. “We see that there are many shades of green, but no one has defined what eco-friendly is going to be. Is it using plant-based materials instead of fossil fuels? Or recycled materials?” Right now, the industry is unsure, but Wohlfahrt believes that will change in the future. “It all depends on what the EPA does,” he says.
Getting a Jump on Repairs
Putting repairs off is never a good idea, despite the temptation in today’s still-uncertain economic times. But with parking lots, ignoring trouble spots and hoping those pavement cracks get smaller simply won’t work. In fact, in the long run, it will only make needed repairs more expensive. “You can defer things for only so long,” Burns says. “Eventually, deferred maintenance will catch up with you and deferred maintenance always costsmore than preventive maintenance.”
And it’s fine if not all repairs can be made at once, Swain says. “Most placescan’t do all of their maintenance at once. You might do patching one year, then crack sealing the next. The important thing is to be proactive and stay on top of things.”
Making repairs in a timely and efficient manner also will help managers and boards avoid, or at least put off, the end of their parking lot pavement’slife. “When it’s too far gone for seal coating or by the time you reach the point where cutting and patching would cost more than repaving it,” you know the lot is done, says Swain.
But with the right planning, that day can be decades away. With good maintenance and preventive care, says Burns, the dividend can be an extra 10 years on the life of your lot. And for condo managers and boards, that is an extra decade of happy residents walking and driving on clear, safe pavement.
Liz Lent is a freelance writer and a frequent contributor to New England Condominium magazine.
Leave a Comment