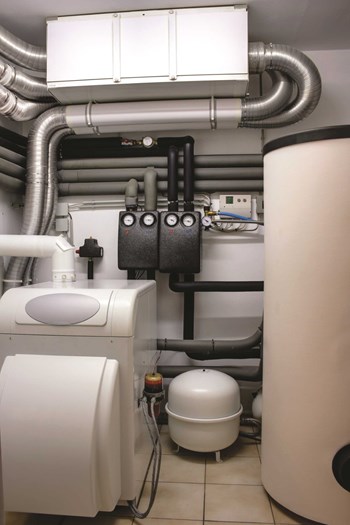
The rarely stated—but all too well understood—Murphy’s Law for Boilers— asserts that if your boiler quits working, it will do so on Christmas or New Year’s Eve, or at 4:45 p.m. on the coldest day of the year. With some planning, though, that broken-down boiler won’t be yours on those inopportune frigid days. An association’s management and staff can head off a worst-case scenario by scheduling regular maintenance and keeping an educated eye on the whole system.
To avoid that irksome phone call to a technician—along with everyone else whose boiler seems to have “picked now” to stop working, a little maintenance goes a long way and breakdowns are preventable. Understanding a boiler’s life expectancy and tending to boiler maintenance can avoid the no-heat nights (and days) that seem to happen at the most inconvenient times.
You know the old saying in real estate, “location, location, location?” For boiler care, it’s (the admittedly less catchy) mantra of “maintenance, maintenance, maintenance.” Lack of routine, preventative maintenance inevitably leads to problems, says Phil Renzi, senior property manager at Thayer & Associates in Cambridge, Massachusetts. Don’t just “turn it on [when the season starts] and expect it to run,” he cautions, because he has seen the aforementioned scenario play out many times before. So much of what happens in an emergency situation is not, in fact, an emergency—or needn’t be, if cautionary steps are taken in advance.
Maintenance Musts
Boilers are durable for many decades—or used to be, anyway. Vintage matters: Steven Dannin, president of Dannin Management in Brookline, Massachusetts, says in his experience, older boilers have a longer life span. “In the past 20 years,” he says, “I’ve replaced boilers that were 30 or 50 years old. In our last project, we took out two 50-year-old boilers. The newer ones are more efficient but the older boilers were built to last.”
David Barrett, who serves as director of operations for Crowninshield Management Corporation in Peabody, Massachusetts, adds that the high-efficiency stainless steel boilers that have emerged recently last about 25 years. Although the boilers themselves don’t last as long as the cast iron ones, the savings in fuel costs offset the shorter life expectancy. That being said, the boilers “have to be run at the proper temperature as suggested by the manufacturer, or they can decay prematurely.”
Renzi, Dannin, and Barrett all agree, and emphasize, the following: Boiler maintenance should be at least annual for condos of all types, ages, and sizes. Renzi says in that in some of the new mid-rise condos his company manages, every unit has a pump for heat as well as for air conditioning. A tune-up is usually the owner’s responsibility, but the proscription remains the same whether a boiler services one unit or an entire building: “We highly recommend that those with individual heat pumps do maintenance twice a year and a filter change every few months.” Townhouse condo owners are also responsible for their own units, says Barrett, and he suggests annual inspections with efficiency in mind. The cleaner a boiler is, the more efficiently it will burn fuel—and thus, the more cost effective it is to run.
Note the use of “recommend” rather than “require.” Most boiler systems are not required by law to have scheduled inspections; nevertheless, Barrett again stresses that “being proactive avoids costly breakdowns.” Renzi notes that for safety reasons, Massachusetts requires steam boilers to undergo an annual pressure vessel inspection for leaks and ruptures. The state’s Executive Office of Public Safety and Security conducts the inspection and issues a special Inspector of Pressure Vessel license. (OSHA defines a pressure vessel as a “storage tank or vessel that has been designed to operate at pressures above 15 p.s.i.g.”.) Insurance companies, too, inspect steam boiler systems once a year for certain kinds of policies.
Life happens, though, and good intentions sometimes fall to the wayside. To avoid the oversight of an annual inspection, Barrett recommends getting a service contract. Moreover, for some systems, even a yearly once-over might not suffice. Renzi suggests checking the owner’s manual, which may advise more frequent upkeep: “It really depends on the manufacturing guidelines,” he says, “like a car. Confirm exactly what you should be doing and how often.”
Without a doubt, preventative maintenance makes sense, even if we’re often accustomed to treating a problem rather than averting one when it comes to home and building repairs. According to Dannin, sometimes condo boards don’t have an adequate understanding of what the boiler maintenance process entails. As a result, they risk making the mistake of contracting technicians to perform “cursory service rather than thorough service.”
One Size Fits All?
“Routine maintenance” doesn’t have a one-size-fits-all checklist because, as with other aspects of managing boilers, it depends on the system and the type of fuel being used. At a minimum, circulatory pumps and heat exchangers should be cleaned yearly. Water treatment is also important to prevent sediment accumulation and corrosion.
Different systems require different licensing and certifications (gas boilers, for example, are often serviced by plumbers); even inspecting pressure vessels requires a specific license. Barrett, who actually holds a license as an oil burner technician, says oil burners should have an annual tune-up. He adds that gas boilers’ components should be checked during maintenance and that forced hot air system filters should be changed several times a year.
Building superintendents and property managers need not—and should not—rely completely on outside services, says Dannin. “Even the unskilled eye can see a leak, even if you can’t identify the source or fix it.” That’s not to say anyone without expertise should go poking around the boiler; only a professional should do repairs or open up anything. However, in Renzi’s view, supers and managers should be in the habit of checking gauges regularly to “make sure they are within operating parameters—things like where the pressure should be, and so on.” Dannin echoes this idea, encouraging management responsible for steam boiler systems to check water levels weekly. The system shuts down if the water level is too low; not enough water also puts the boiler at risk for melting.
Boilers with a Brain
Being observant, then, is part and parcel of maintenance. Keeping a log of self-inspection activity helps, too, and it’s a good way to track patterns over time.
Boilers these days, like kids, are smart; even they play a role in preventative maintenance. That is, sometimes the boiler itself will tell you when to call in the pros. High efficiency boilers, Renzi explains, have a built-in notification system for maintenance. Those kinds of boilers will actually shut down in the event of a malfunction; it’s a safety measure designed to stop a problem before it becomes a larger one.
The “avoiding inopportune moments” objective has two parts. The first is a regular boiler inspection. The second is when to have it. Dannin, Barrett, and Renzi each make it clear that having boiler maintenance prior to cold-weather season will save plenty of headaches (not to mention money—emergencies at night, on the weekend, and over holidays are especially costly). The best time to have everything examined, therefore, is right before you really need the heat to be on. Even if the boiler works, it doesn’t hurt to have a dress rehearsal. As Dannin points out, you want boiler systems “to run for a bit before you test their efficiencies.”
Some properties, Barrett says, have cooling and heating systems paired together; in those buildings, the drill is usually to do maintenance on all systems during the switch from cooling to heating. Renzi’s company begins the process in August or early September, because per Massachusetts law, property managers must have heat available in the units by September 15.
As for what constitutes a common repair for a boiler system, as with many other recommendations, it’s determined by the type of fuel used. Dannin offers a few examples: For oil and gas, it’s often the safety controls because they don’t burn as cleanly. Forced hot air systems, by contrast, control their functions based on the weather. In New England, certain settings are suitable for winter, others for spring and fall; this can vary greatly when the goal is to balance the system based on the outdoor temperature. Sometimes, Dannin adds, “climate control systems are finicky.” Water leaks, too, are a problem—and a good example of how a minor issue can become a major one if it isn’t addressed. If a boiler’s tile insulation cracks, it’s often the result of water leaks.
Keep in mind that when all is said and done, even with regular maintenance, boiler problems can still arise. Parts can just wear out, Dannin says. Sometimes that alone shuts down the system at the dreaded “inopportune time.”
At least you’ll know who isn’t responsible for the overtime call to the technician. Sorry, boiler. This one is on you.
Jodie Lynn Boduch is a freelance writer and a frequent contributor to New England Condominium.
Leave a Comment