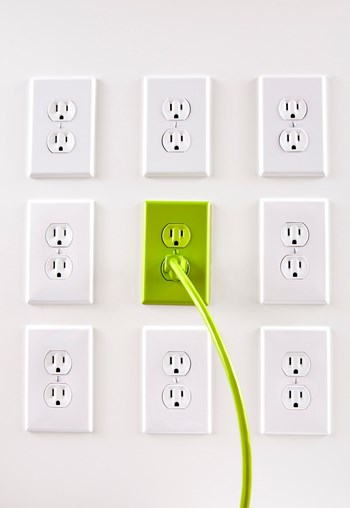
Yogi Berra, former philosopher-catcher for the New York Yankees, got it right. “It’s déjà vu all over again.” The reprise of the 1973 energy crisis is back on stage. The future is not what it used to be. Energy is the new arbiter of economics and, it would appear, global politics. The U.S. Department of Energy reminds us (again) that residential buildings consume 21% of the nation’s energy menu. We know that common interest developments make up a significant andgrowing portion of that percentage.
Previously, clients putting up a new building might look at higher initial construction costs for energy reduction and say, “No thanks.” The modest down-the-road return on investment (ROI) would not get their attention. The new ball game with higher energycosts has shortened up the ROI. Still, “green” programs like Leadership in Energy and Environmental Design (LEED) speak purely to new designs for new construction.
But what about the inventory of existing buildings — the ones continuing to consume that 21%? Can they be retrofitted to reduce the rising costs of heating and cooling them? The short answer is yes. But it is up to us to figureout how to do it by adapting the technology and management at hand.
Unique Position for Savings
For those of us working with common interest developments, it turns out that we are in a unique position to reduce the ever-rising cost of heating and cooling our buildings. The technologyis textbook stuff. The management, though, needs some development because this is relatively new territory.
First, the technology. Three possibilities present themselves for reducingenergy consumption: insulation, air movement and heating source. Let’s work through an example to see what the potential might be.
Assume we have a two-level, inside townhouse unit, 38 feet wide by 38 feet deep. It is heated by an oil-fired furnace. It has an average number of windows and doors, one of which is a glass slider to the deck. There is 3½ of fiberglass in the exterior walls and on the attic floor.
Reducing Conductive Losses
Thermal energy moves from areas of high activity to those of low, from warm areas to cold areas. The speed with which it moves depends, primarily, upon the difference in temperature between the indoors and outdoors and the nature of the building surfaces. Insulation like fiberglass, because of its matrix of fibers, offers resistance (R value) to that energy movement called conductive heat transfer. More insulation, more R, less energy loss over the same time period. In our example condo unit, we are going to blow 8 inches of fiberglass onto the attic floor to increase the insulation thickness to 11½. We’ve increased the R-value of the attic floor by a factor of 2.5. That means a corresponding reduction of conductive energy transfer.
As much as 40% of winter fuel consumption can be spent warming the cold air that comes in around leaky windows, doors and joints in the building envelope. The latest techniques in new construction provide intact barriers to air movement through the exterior envelope. While back-fitting of the air barrier is not possible in existing buildings, cold air infiltration can be defeated by sealing (caulking) around window and door frames. We’regoing to seal around the perimeter of all the windows and doors of the example unit to achieve a reduction in cold air infiltration of 65%.
Heating/Cooling Plant Efficiency
The target here is to increase the Annual Fuel Utilization Efficiency. A competent HVAC analyst might well identify modifications to an older furnace that would increase AFUE by 15%. This might be achieved through replacement of the oil burner and control devices – not a significant investment.
To summarize:
BTUH = British Thermal Units per Hour of heat loss
Assuming No. 2 fuel oil selling at $4.70 / gallon, the savings to our unit owner would be about $1,000. The project would pay for itself in 2½ heating seasons. After that, continual savings accrue. The added insulation and reduction of air entry would reduce summer electrical power demand for any cooling equipment in place. What about new energy sources? Our firm is investigating using solar collectors for heating domestic hot water, essentially water used for washing. This could further reduce costs. So we’ve made a modest investment for an acceptable ROI with a potential for more.
Governance in Action
The exterior envelopes of buildings — the major players in energy transfer — are commonly owned. The fuel billsfor the energy needed to neutralize that transfer are addressed to the unit owners who live within the unit boundaries. Clearly, some form of interaction is needed to make projects similar to our example happen.
The board or association management would need to do for the unit owners what they cannot, by definition, do for themselves. A community-wide project would enjoy the economy of scale. Bids could be expected to respond to the repetitiveness of the building configurations. There would seem to bemore than sufficient economic justification here for finding a workable management model.
Funding for such projects might be done through an existing capital reserve fund or separate capital improvements program. Tax credits, like those in Massachusetts, are presently available to encourage use of renewable energy sources such a solar thermal and photovoltaic. It would seem reasonable to anticipate federal tax credits as the benefit of retrofitting existing buildingsbegins to demonstrate itself.
Innovation typically follows a challenge. There is more than sufficienttalent in the community association industry to meet this one. Or, to quote another Yogi truism, “It ain’t over till it’s over.”
Bob Burns, RS., PE, is the president of Burns and Associates – Engineers, in Portsmouth, New Hampshire.
Leave a Comment