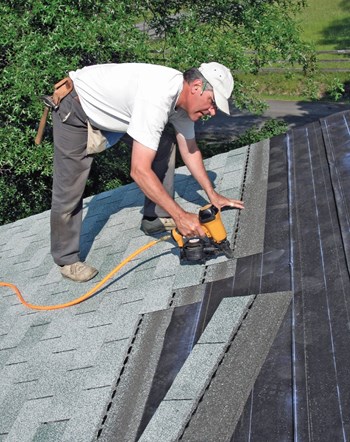
The roof carries a lot of responsibility – it protects those living inside it, insulates them from the heat and colds and shelters them from harsh New England winters. And it’s because of these major responsibilities that it needs to be inspected, repaired and cared for on a regular basis.
Without regular checkups, the roof can crack, break and leak. “You may have heard that money is the root of all evil, but in buildings, water is the root of all evil,” says Russ Fernandes, principal at Becht Engineering. “Water that is not kept out of buildings via proper roofs and facades and their associated components, will ultimately end up with the building’s owners having to pay large sums of money. These expenditures can often be avoidedor minimized through proper, timely inspections and repairs.”
When Old Man Winter makes himself at home, water can also enter a building through ice dams which form when water builds up behind a blockage of ice on the roof. “I would suggest that 90 percent of the time, roofs leak in the winter because of ice damming,” says Paul Martin, a senior project manager at Noblin and Assoc-iations LC, Consulting Engineers in Bridgewater, Massachusetts. “Roofs also have problems because of inadequate ventilation. A hot attic can age roofing shingles.”
Types of Roofs
There are several common types of roofs in the New England area – shingle, PVC, and rubber, the most common. Most flat roofs are made of rubber, also known as EPDM (ethylene propylene diene polymethylene) membrane. According to the EPDM Roofing Association, rubber is great roofing material for harsh new England winters because it’s resistant to UV (ultraviolet) radiation, has unmatched resistance to thermal shock, exhibits superior resistance to cyclic fatigue, hassuperior resistance to hail damage, and will not become brittle or shatter due to low temperature flexibility.
“This is perfect roofing material to protect against harsh New England winters that are accompanied by severelycold temperatures, intense winds and the weight of snow,” says Martin.
PVC membrane, also for flat roofs, is composed of only one layer of material, polyvinyl chloride. PVC is welded together with hot air to eliminate seams so moisture can’t pass through. PVC roofing systems also reflect nearly 90%of the heat of the sun, thus lowering energy costs substantially, especially in high-heat areas such as the southwestern United States.
“The difference between EPDM and the PVC is that the PVC heats the seams together, but the EPDM glues the seams,” says Martin. “Because you weld the seams there is more quality control. It becomes a monolithic surfacebonded to itself and almost becomes a single sheet. The rubber roof, when it fails, it fails at the seams. If the draining on the roof isn’t optimal, the water will degrade the seams.”
Asphalt shingle roofs, for sloping roofs, can last for quite some time – up to 30 years – while other shingle roofs need replacing after only 15 years. “There was a premature aging of shingles that was very prevalent about a decade ago,” says John Turner, president of Criterium-Turner Engineers, with offices across New England. “We’re still seeing cracking from asphalt shingles that’s mostly attributed to problems from expansion and contraction. It would be hot during the day and cold at night, but instead of expanding and shrinking, the shingles are splitting. It’s a serious case that can go through multiple layers.”
Annual Inspections
With all the problems that can happen to roofs, and how costly they can be to replace, annual inspections are recommended, but depending on the configuration of the roof, more may be needed, especially after major weather-related events.
“For example, the lower the pitch of the roof, the more often it needs inspection,” says Turner. “Remember, too, that you could put a brand new roof on in the summer, but if we have serious ice dams again we could have significant damage due to the dams or the removal of them.”
Don’t just have the roof inspected though, says Fernandes. “Flat, membrane-type roofs, as often found on high-rise buildings, require close inspection of not only the roof surface but also the integrity of flashings, penetrations and bulkheads.” Flashings are waterproof membranes or sheet metal that is installed around windowsand doors or any break in the roofline to help prevent leaks. They are also installed around sewer vents and chimney flue pipes. Bulkheads are structures on a roof that cover a stairwell or other openings.
“We recommend that an infrared scan be performed every three to five years to check for moisture below the roof surface. Found early enough, repairs can be made that will prolong the life of the roof,” says Fernandes.
A roof inspection should be part of the building’s annual maintenance plan. Although management and staff can perform a visual inspection of the roof, Turner says, “you need a professional who can recognize very subtle changes in the roof. You have to see any premature aging up close. You should usea registered roofing consultant or a trustworthy contractor.”
“A registered roofing consultant takes classes and becomes certified. It says that you’ve invested in learning to become certified and evaluate the roofing,” says Martin.
During inspections, inspectors will notice if parts of the roof are starting to fail or if there has been damage. “In a flat roof, we’ll look to see if the seams in a membrane and adhesives are starting to fail,” says Martin. “We’ll look for connection details and make sure drains on a flat roofing system are cleared. With a shingled roof, you’re looking for wind damage – shingles that are blown off because they’ve been impacted by something. The wind is a killer here for shingle roofs.”
Repair or Replace?
Once the problems are apparent on a roof, a board and management will need to make the decision to repair or replace it. There are several factors thatgo into making that decision.
“Roofs need to be repaired or replaced for a number of reasons, ranging fromnormal wear and tear due to age, to physical damage and/or improper initial installation and design,” says Fernandes. “If a flat roof is intended to host extensive foot traffic and/or sundecks, the roof has to be designed for that purpose, as most typical membrane systems are not intended for foot traffic beyond an occasional service person.”
He also explains that a five-year-old leaky roof would just need to be repaired, but a 20-year-old roof with the same problem has likely met or exceeded its life expectancy and wouldbe a candidate for replacement.
Another factor is the cost of the needed repair as compared with the cost to replace. “In general, if repair costs are approaching half the cost of a full replacement, full replacement should be considered,” says Fernandes. “Keep in mind that repaired areas will have to be removed during any subsequent roof replacement, so a board wouldn’t want to spend too much on a repair procedure if the roof is going to require replacement in the near future.”
“For example, there are buildings with dramatic algae – black streaks and mildew – on them,” says Turner. “You can actually install special metal strips that will arrest and stop that growth. Those strips can slow the deterioration on the roofing. By stopping the black streaks and mildew, youcan extend the life of the roofing.”
Another factor that determines whether the roof is repaired or replacedis how many roofs are actually on the building. Many times a new roof is installed over a failing roof to save the expense of “tearing off” the old roof. Fernandes explains that most building codes limit the number of roofs on a building to two.
“Therefore, if a building already has two roofs, it is time for a complete tear-off, down to the roof deck,” he says. “A complete tear-off of a single roof layer might be warranted if the roof has been problematic during its life span. Tear-offs often uncover hidden damageand defective flashing that would not have been found if the new roof was simply installed over the first.”
Roofs are a System
Martin urges boards and management to think of roofing not as just one piece, but made up of an entire system of interchangeable parts.
“Clients save a little bit of money by putting new shingles over old ones, but they don’t think about the flashings and the under-layings,” he says. “You should think of the roof as an entire system. Ridge vents and plumbing ventboots should be replaced. Sometimes it’s possible to do miscellaneous spot repairs on the roof, but if you have a leak and it’s right in the middle of the room, it doesn’t mean that the origin is right above in the roof, so you need to find the flaw in the entire system to make the repair.”
Lisa Iannucci is a freelance writer and a frequent contributor to New England Condominium magazine.
Leave a Comment